Dolcella: the Industry 5.0 revolution in a confectionery specialist company
2024
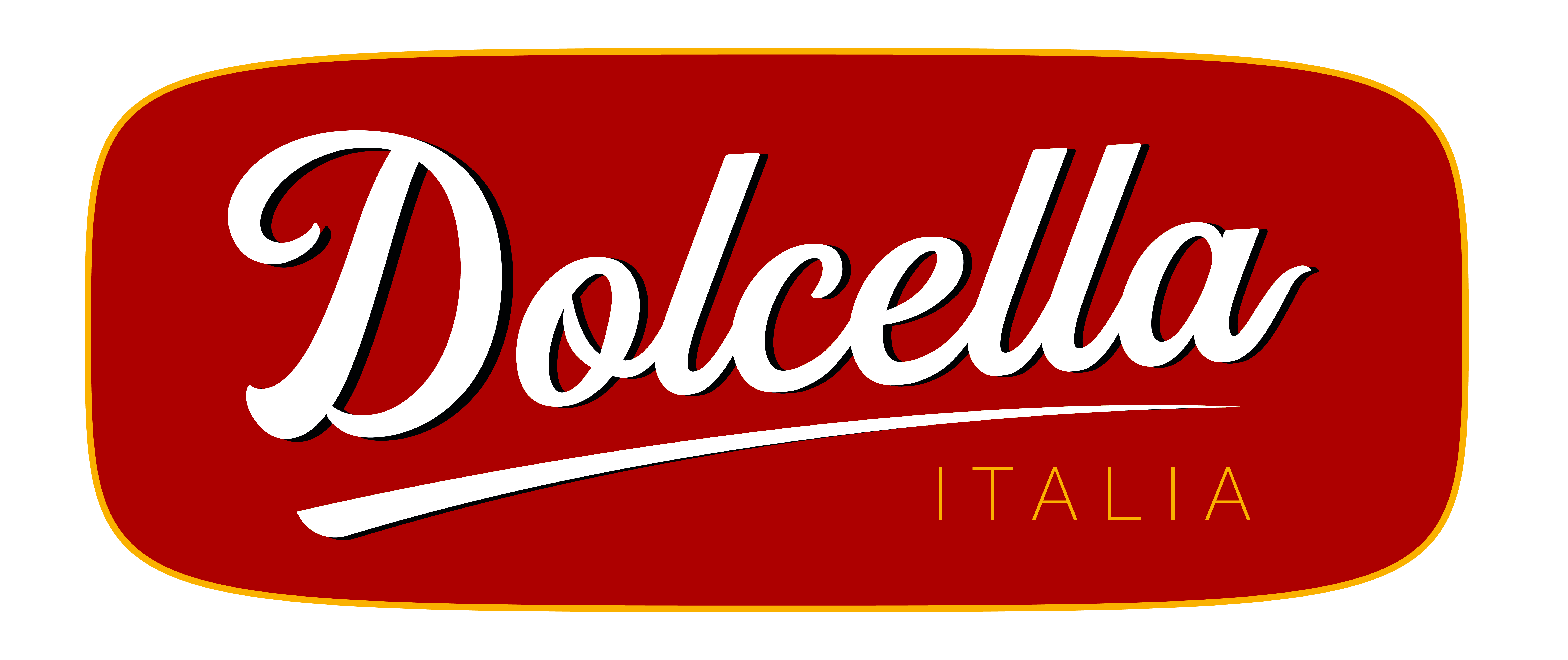
THE CHALLENGE
Dolcella is part of a Dutch holding company in the confectionery sector. The plant, which has been operational since March 2024, is located in Pont Saint Martin (AO) on the site of the former Feletti factory and covers an area of 27,000 square meters, of which 16,000 square meters are covered. As of today, it has a total of 15 employees, including workers and office staff.
The company’s production is primarily focused on chocolate pralines. The daily capacity of the production line, operating on two shifts, is approximately 10 tons. With the goal of satisfying an increasingly broad range of consumers, in 2025, the product catalog will be expanded with the introduction of a production line for cremini.
In 2022, during the redesign and revamping phase of the plant, the company decided to upgrade the new machinery to Industry 4.0 standards by interconnecting two new packaging lines, from single and double twist wrapping machines to bagging machines for the finished product.
This decision allowed the company to access tax credits under the Industry 4.0 Transition Plan and to begin a partnership with Orchestra aimed at transforming Dolcella into a fully digitalized factory.
THE SOLUTION
Dolcella thus entrusted Orchestra with the management of the entire digital project, which is progressively expanding, selecting suppliers for the IT infrastructure and management system, and providing its own technology for the interconnection of production lines as well as the management, monitoring, and control of all processes.
In this phase, Orchestra relied on some of its specialized partners: SHT for the provision of the IT infrastructure and Braindata, which supplied its ARCA management system.
Production is managed by RETUNER®’s miniMES 5.0, a suite of Orchestra products that allows for the planning, tracking, controlling, and reporting of machine operations in production. MiniMES 5.0 connects production operators on any device to track all phases of production, enabling them to monitor activities, downtimes, production progress, and anomalies.
Orchestra supports the expansion of Dolcella’s production activities. By moving to xMES, the extended version of RETUNER®’s miniMES 5.0, Dolcella will be able to:
- Expand the functionalities of the current miniMES 5.0 to additional areas such as outsourcing management, intralogistics, quality control, and maintenance of production assets
- Monitor energy consumption relative to the equivalent production unit to access the benefits of the new Transition 5.0 Plan
In this latest case as well, Orchestra, leveraging its partners specialized in providing certified electronics for energy consumption measurement and consulting for energy analysis and assessments, will provide Dolcella with the new Transition 5.0 Package which includes turnkey services for the client, from managing the process with GSE to the final assessment for accessing the tax credit.
THE BENEFITS
The adoption of miniMES 5.0 with the interconnection of the entire machinery fleet has revolutionized Dolcella’s production process.
“With the use of Orchestra’s MES, we aim to achieve greater efficiency and higher productivity in production control. The automation of production processes allows us to save on labor costs and increase the technical knowledge of our staff,” says Idris Anday, plant manager at Dolcella.